Engineering
State of the art facilities and tools for designing and engineering as well as continual internal investment allows us to provide you with the most up to date know-how on foundry technology and innovative equipment and processes.
GEMCO is an independent company and not under contract to any manufacturer. This allows us an independent approach in the selection of the optimum solution for all equipment for each foundry design.
SMART SOLUTIONS
"...We chose Gemco as our engineering partner. They are highly professional, creative, think with us, and have a profound knowledge of the foundry business and technology ..."
- is what they say about us -
Concept Engineering
Our whole philosophy is focused on providing customized foundry solutions, which stems right from the feasibility and pre-engineering studies of the concept phase. Always working in close cooperation with our clients we establish a bankable report including issues such as:
- Feasibility Studies/Techno Economical Base
- Process Technology
- Process Flow & Logistics
- Foundry Lay-out
- Equipment List
- Utilities Requirements e.g. electrical power, gas, compressed air, water
- Budget/Cost Estimation
- Raw Material Requirements
- Manning Schedule
- Project Time Frame
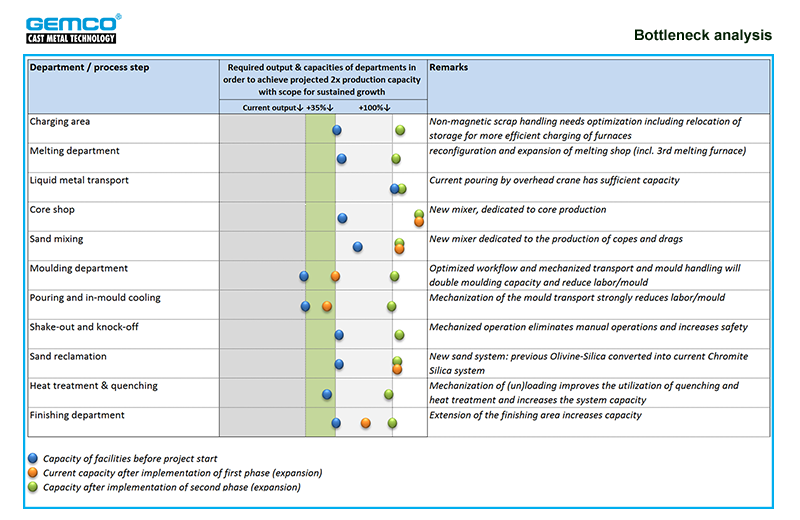
"...Innovations start with people ..."
Project Engineering
After concept engineering and prior to realization, a number of engineering decisions must be taken, including important building/construction matters. Our engineers and different technology experts extend their focus to the many fields that require attention before the realization of a project:
- Detailed equipment specification
- Interface design
- Material flow and logistics
- Foundation load specification
- Building requirements and design
- Utility distribution (electricity, gas, compressed air, etc.)
- HVAC specification
- Data acquisition and plant control
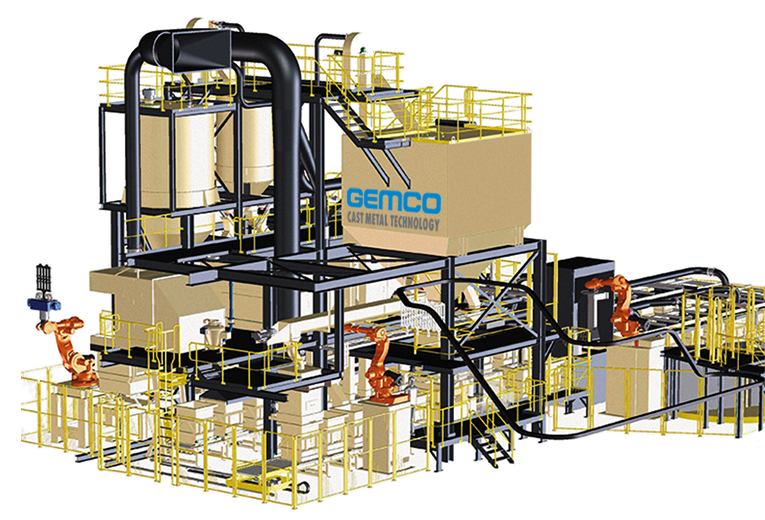
Foundry Simulation
Foundry Logistics Simulation supports the engineering process in our more complex projects to determine the optimum foundry. Gemco’s simulation engineers create 3D models that run the actual or future client’s production program, giving insight in the process flow, utilization rates, potential bottle necks and ‘what happens if …’ scenario’s.
This 3D insight is not only static: it shows the running foundry that produces the customer's products according their production schedule.
We have applied simulations on a wide variety of engineering challenges such as the design of a 100t-h scrap yard, logistical optimization in the production of 7 meter long railway crossings and the molten supply in a foundry with 10 continuous casting lines.
The Foundry Logistics Simulation tool was developed in close cooperation with the Technical University in Eindhoven (TU/e) and the University Twente (UT). It has enabled us to realize the most efficient and reliable solutions for our customers.